Check this Out
Hydraulic Symbols Template
Try the Ultimate Beam Calculator
Schedule Time with Corey
Recent Posts
IIoT Terminology with Sealevel Systems
What Does a Mechanical Engineer Actually Do? – 9 Career Paths
If you’re interested in becoming a mechanical engineer you may be confused and overwhelmed because you are unclear of what a mechanical engineer does.
From a very early age, I knew that I wanted to design and build things for a living. This started when I was a kid playing with Lego. I really made some tall cranes and interesting machines. That is why I chose to become a mechanical engineer.
Mechanical engineers play a role in the design, production and distribution for nearly every product in you home. They design cars, airplane, robotics and industrial machines. They also research new materials and investigate failures and accidents. Mechanical engineers will also work with engineers of other disciplines as well.
First off, an engineer has nothing to do with driving a train! (much to my disappointment; I love trains!).
No, an engineer is a problem solver so you must love solving problems above all else.
Mechanical Engineering has the widest scope of any engineering discipline. With civil engineering, you know that you are going to work on roadways and bridges with a large emphasis on how they interface with the ground. Electrical engineers will work on electrical components.
The story is quite different for mechanical engineers. In school, you will study three main branches of mechanical engineering, thermodynamics, fluid mechanics and solids.
I believe that a fourth will be added within the next ten years, mechatronics. Mechatronics is the combination of computer science, mechanical and electrical engineering for use in integrated systems. Robotics and automation are great examples of how a mechatronics degree would be used.
With such a wide scope in mechanical engineering, no one can master more than one area and you can specialize in very small niches if you desire to.
Areas of Mechanical Engineering
Thermodynamics
Thermodynamics is the study of materials and how heat effects them. These materials are not only solids, but gases and liquids as well.
Engineers who use thermodynamics enjoy careers power plant design / management, HVAC (Heating, Ventilation and Air Conditioning), combustion or cyrogenics.
Fluid Mechanics
Fluid mechanics is a very interesting branch of mechanical engineering. We can probably guess that they study how water flows in pipes, but it in no way stops there.
For me, it gets confusing when we consider how fluids flow over surfaces like a boat hull through water, airplane wings through air or a parachute coasting down to earth.
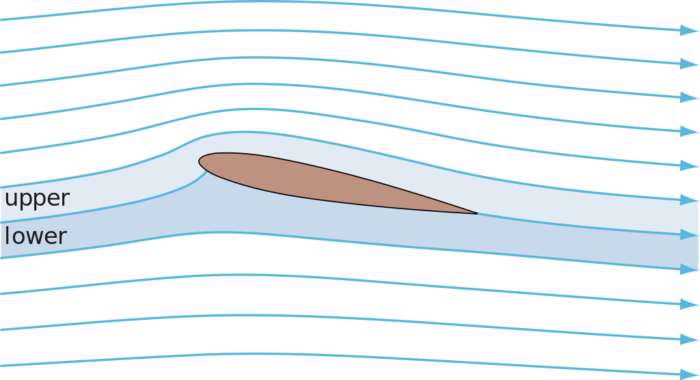
I’m totally lost when the fluid starts getting compressed and you can control the gases expansion in a combustion process to create thrust. Yes, fluid mechanics play a large role in rocket design.
Hydraulics is another large section of fluid mechanics. Many engineers that work with mobile or industrial equipment will cross over into this field to actuate mechanical functions. There is a lot of design effort that goes into designing valves and valve systems.
Solids / Structures
Solids is a very vague term to discuss this part of engineering. It is sometimes called structures, but that is also misleading because it is often confused with structural engineering. That is the structural design of permanent things like buildings and bridges.
This is my area of expertise and it generally can be defined as anything that is solid in nature, but not permanently attached to the ground. Good example are automobiles and other types of mobile equipment, industrial machinery, tools, alarm clocks, computer cases, metal furniture etc.
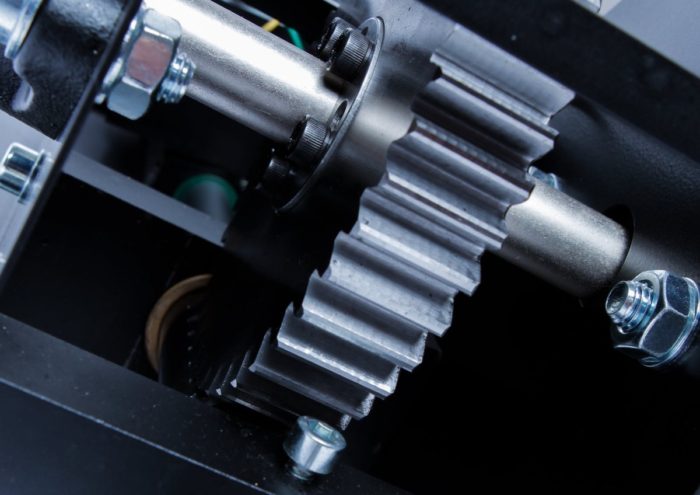
A solids engineer will evaluate stress and strain on an object and determine if it will break or not. Often times, the engineer will need to estimate loads and load cycles when they are not clearly defined.
Mechatronics
Right now, it appears that mechatronics is an engineering discipline just for graduate school. You may be able to take some electives for your undergraduate degree.
Mechatronics will be a growing field of study for years to come. The ability to design both electrical, computer and mechanical systems is only at the beginning stages.
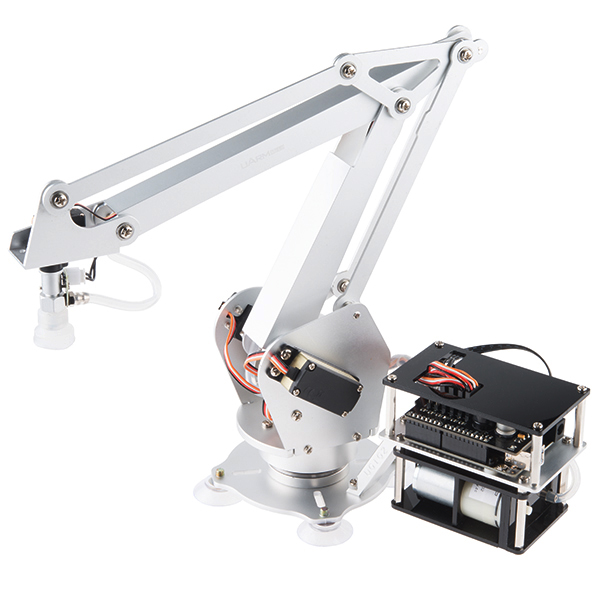
One area of mechatronics is the IoT or Internet of Things. This is the technology that allows us to remotely start and stop our cars, lock the doors on our house and check on our kids when they get home from school.
One large subset of the IoT is the Industrial IoT (IIoT). This applying sensors to machinery to determine machine up time, report signs that parts are worn out and need to be replaced etc. Since more and more production will be automated, keeping machines running at full capacity will be critical. We will need lots of engineers to keep these running.
Career Paths
1. Design
So the design engineer is probably the most prominent and sought after roles as an engineer. Everyone wants to design something! A design engineer will need to be able to brainstorm, conceptualize and bring multiple systems together to work as one. These are not easy tasks.
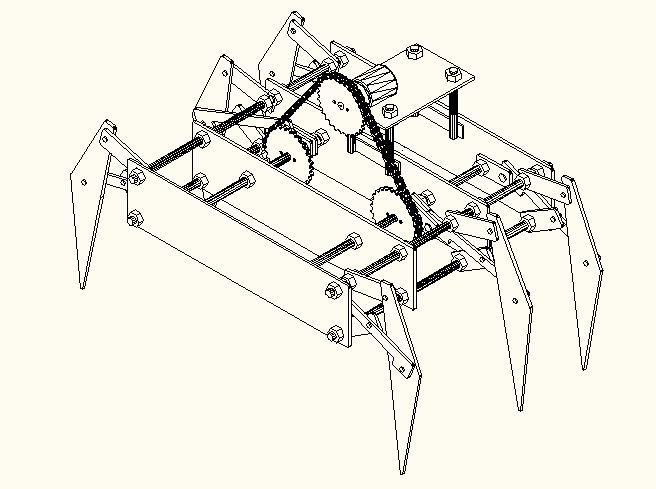
A good design engineer will need to be good with all types of stress calculations, analyzing stress flow and finding ways to approximate things that are impossible to calculate. Another necessary skill is to be able to mentally see how a design works in time (the 4th dimension)
2. Testing
The testing engineer is the design engineers worst foe and the company’s best insurance policy. No one wants to launch a product that has a fundamental defect or doesn’t operate as intended.
Test engineers are responsible for examining products and / or software and finding ‘real world’ ways to break them or at least make sure they will last for the intended lifespan.
Test engineers will need to develop methods of testing products that may require high loads or cyclical loading patterns. You can also find out how to test for operation in high / low temperatures and weather conditions (mostly water).
3. Sales
Once you have a product, you need someone to sell it. Sales engineering will meet with customers to determine what the customer’s goal is and to suggest products that will solve their problem.
An engineering background comes in very handy here because you be able to grasp a full understanding of the product and what the customer wants to do. If you don’t know how a particular part of the solution would work, you are more likely to be able to identify this and bring others in who can answer the question.
If a non-technical person is in this role, you may sell a lot more product at first, but if it doesn’t meet the customer’s goal there won’t be any repeat business. You always want to make the customer have a pleasant experience so having a sale engineer is often the better choice.
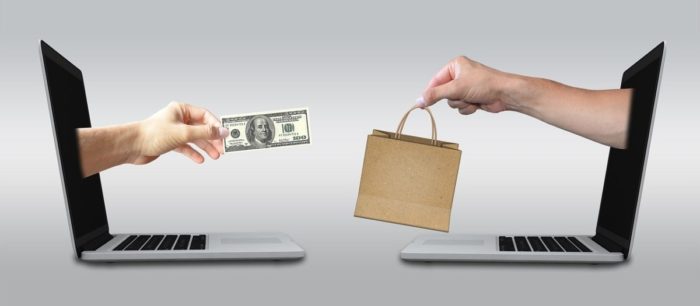
4. Applications
Because of the complexity of equipment that is on the market, many mid to high end product are not purchased, but applied. This is where the applications engineer comes in.
The engineer will usually meet with a customer and salesman and do a thorough investigation of what the projects goals are and how to accomplish them. They will ask probing questions to make sure that the potential product is exactly what the customer needs.
After the sale, the applications engineer will customize an existing product(s) to the customer’s requirements. Sometimes these solutions will be fairly intense. The end result is a system that will not only meet the customer’s expectation, but it will also be a complete solution.
Applications engineers usually like this position because it allows them to meet with real people and get away from the desk. Applications engineers that interface with customers on a regular basis usually have a good idea of where their industry is headed.
Good examples of systems that are applied and not purchased are valves and valve systems, electronic control systems, fabrication machinery or any other product that has a multitude of options.
5. Investigative
An investigative engineer will travel to locations where accidents have occurred. These engineering can work for a private company, an insurance company, law firm or government agency.
The engineer will gather information from the accident and try to determine the cause of the accident for the purpose of trying to prevent it from occurring again.
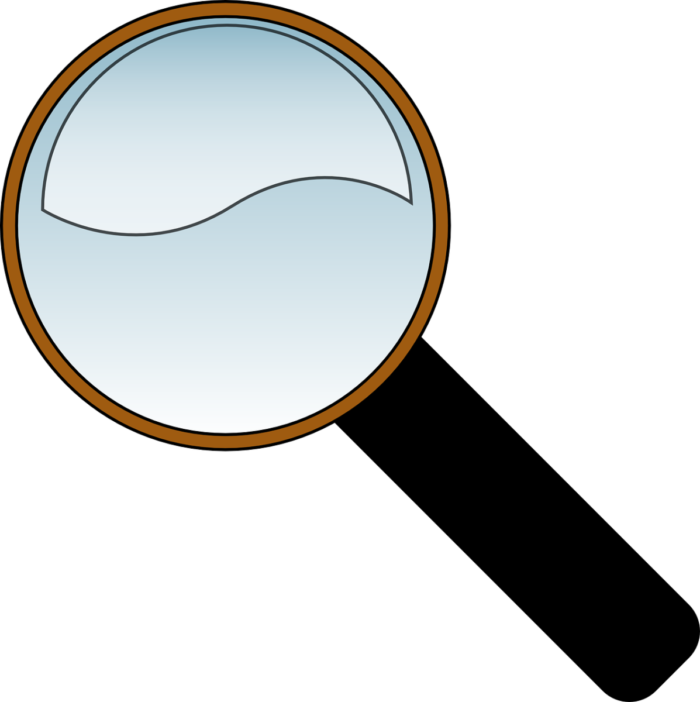
This an exciting area of engineering because one failure will teach you more than a thousand successes. If you want to be an investigative engineer, you first need to be competent within your discipline and you better like flying, a lot.
6. Inspection
Similar to an investigative engineer, and inspection engineer will travel around, usually more local, and inspect building, construction sites etc. I generally get an email every quarter asking me to become a roof inspector for commercial buildings
Unlike an investigative engineer, the purpose of this position is to make sure that OSHA and building codes are being met so that there, hopefully, isn’t a need of an investigative engineer later.
7. Research and Development
Research is a critical part of sustaining a business. Many businesses are profitable for a time and then the market shifts leaving them broke. Having a team of research engineers and keeping an eye out for market shifts is important.
Many engineers are interested in being researchers because they will always be on the cutting edge of new technology. The greatest opportunity for a mechanical engineer in this field is in the mechatronics and materials arena.
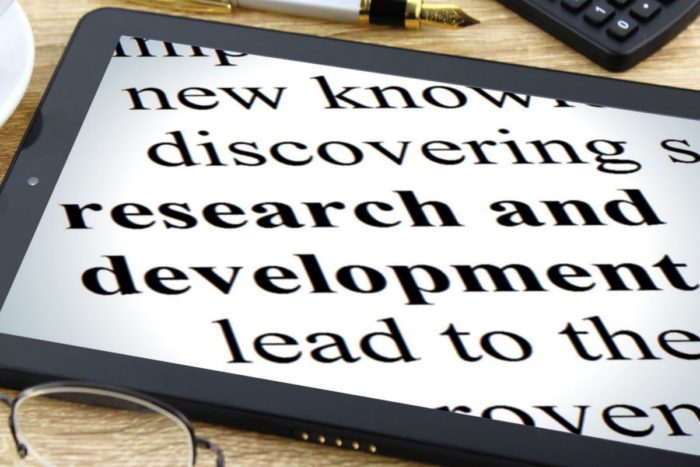
Development is a slightly different from research even though they are usually lumped together in the R & D department. Though they are lumped together, they are not the same. I am a strong developer, but a so-so researcher.
A developer will usually build on the fundamental blocks of the research engineer and take a new product from a concept to production. This type of work has (hopefully) clear objectives, a firm timeline and project managers.
A developer is responsible for making sure that a company is putting out products that will keep them in business many years in the future.
8. Management
The general career path of an engineer starts in the weeds doing more technical work and tends towards management. Generally speaking, it earns more money and at the rate that technology changes, it is difficult for even the most eager engineer to keep abreast of it long term.
There are two main types of managers within engineering, people managers and project managers.
People managers will oversee other engineers and drafters in a department. Many engineers may thrive here but the opposite is true as well. It is always a benefit to have a manager that is an engineer because he or she can relate to the team on a technical level. They also should have better communication skills to relay information to management and customers.
Project managers (PM) are there to keep projects on time and in the money. PMs love Gantt charts and checking bank statements to know when a project is behind or over budget (they all are).

Having a PM that is an engineer is a big help to the development team. I once had a non-technical PM who routinely pulled me aside to ask me basic technical questions. Great every once in a while, but annoying when it is three times a day on a two year project.
9. Consulting
Once you have gained enough experience, a professional engineering license and a ton of contacts, you may think about starting your own consulting firm like me.
Consulting allows you to step out of your main industry and help others with their problems. Some companies just don’t have the knowledge resource or the man hours to start or finish a project. Many projects get dropped if they are small when they run into a technical blip.
As a result, many clients only need a few hours of your time to solve their problem. Other clients will want to hire you full time.
I like consulting because it allows me to work on a variety of different types of equipment and meet with people more. However, the down side is that you have to find clients and manage the entire project process. I highly recommend outsourcing part of this work to a virtual assistant (VA).
In Summary
Mechanical engineering is a very wide discipline with many unique ways to have a successful career. There really are no limits except for the limit you put on yourself.
General IoT Administration Functionality with Sealevel Systems
Proper Tab and Slot Design and How to Avoid Serious Issues
Steel design seems to be moving in the direction of self-fixturing where the weldment or assembly components will align with each other. When a tab or slot is added to a part, the stress flow is disrupted. These can lead to large stress concentrations. Tabs and slot joints should not be added in an already high stress area. Besides removing material, sharp corners in the slot can lead to high tensile stresses.
The reason self-fixturing has become so popular is that it removes lots of time from the assembly process. At a former employer, young manufacturing engineers designed a desk that was assembled using slot and tab design. The tabs had hooks on them so that once they were assembled, it would stay that way.
The design was pure genius: a desk that was made of laser cut sheet metal which could be completely painted in the powder coat system and assembled in minutes with a handful of screws. As a result, almost all desks on the shop floor where this design.
Self-fixturing has become very popular in welding as well. If components can fit together without external fixtures, there is a lot of time and money saved. If you can’t do self-fixturing, try having the fixture be self-fixturing.
Big Changes
Forty years ago, most components were cut in a shear press so designers could never dream of anything approaching tab and slots. It is only with the advent of CNC machining that self-fixturing is possible. New machines like laser and plasma tables or water jets have made this a reality.
Another change has happened just recently. In 2018, Solidworks added a “tab and slot” feature in the sheet metal menu. This allows the user to drastically speed up the process for the designer to add these features. Undoubtedly, this will lead to the proliferation of potential stress concentrations.
Did We Forget About Stress Concentrations?
Yes! Every tab and every slot carries several stress concentrations with it. The slot is most obvious with the 90° corners. But the tab can also have stress concentrations where it attaches to the parent material. These show up when the tab is in tension or bending on the weak axis.
The Battle
In every tab and slot design, there is a battle waging. On one hand, you have a tight fitting joint with only a few thousandths of play. With this you also have very small or nonexistent radii. Very large stress concentrations.
On the other hand, you have a loose fitting slot with radii that minimize the magnitude of a stress concentration.
As the designer, you will need to come up with a balance for this problem.
How to Properly Design Weldments: A Course for Engineers
Stress Flow and FEA
Unfortunately, stress flow is not something that can be easily taught in engineering school. It must be learned through years of practice. This is part of the reason that I am putting together a comprehensive course on stress flow available in the summer of 2020.
The common thought process for young engineers today is to shortcut the learning process by using FEA. There are at least three problems with this.
- FEA only shows you the result – It is important that the designer completely understands how stress flows. FEA is a very slow teacher and the lessons are forgotten quickly.
- The feature is left out – Most designers will leave these features out of the FEA model to speed up run time.
- Singularity – Most designers won’t spend the time to address the singuarity issue in the corners of the slot. FEA doesn’t handle stress making sharp angles well. If the FEA operator is not careful, the stress can be grossly underestimated or overestimated.
Not All Slots Are Equal
Longitudinal and Transverse Loadings
When adding slots, you will want to ensure that your slots are longitudinal, parallel, with the direction of stress flow. In the generic example below a plate is subjected to a 2000 lb load longitudinal to the flow of stress. You can see that most of the stress around 3 ksi. The peak load of 5 ksi occurs in the corners of the slot. The plot shows a fairly even distribution of load around the slot and through the material as a whole.
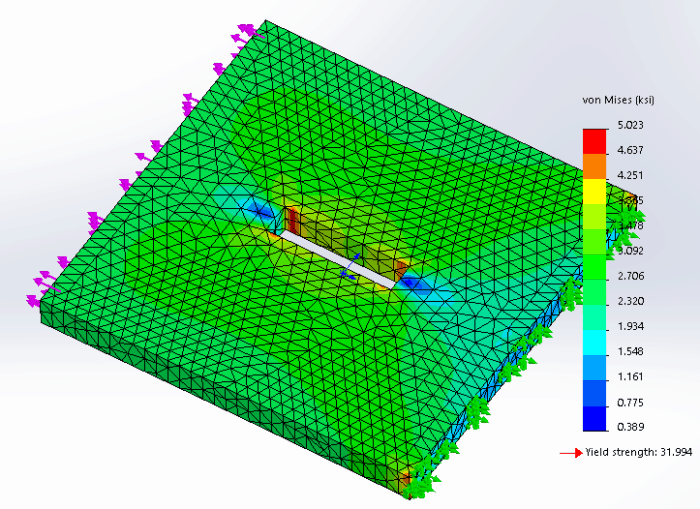
If we rotate the slot (or loading) so that the slot is now transverse, perpendicular to the stress flow, we get much different results.
Our nice, evenly loaded plate now has very hot and very cold spots. We also changed the peak stress to over 10 ksi! Twice as much as the longitudinal peak.
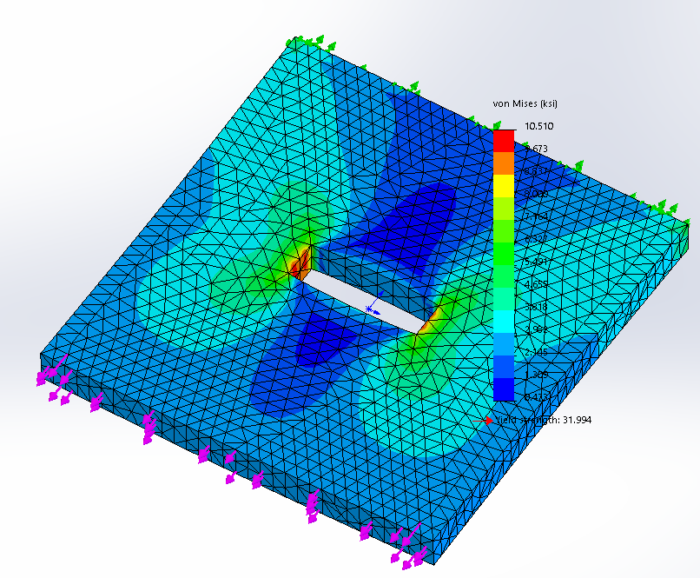
The logical conclusion is to avoid transverse slots as much as possible. It may be necessary to have two or more narrow slots instead of one longer one. As a rule of thumb, I would use the tabbed plate thickness as for the target slot width. This would make a square tab.
Radii Slot Designs
Adding radii in the corners of your slot are a must. This is where FEA and logic don’t meet up because of the singularity issue in FEA. Above, the maximum stress is 5 ksi, but when I add the radii in the corners, the stress increased to nearly 8 ksi.
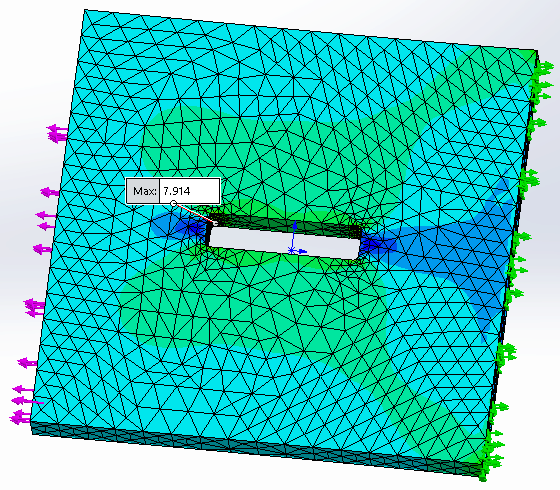
In fact, as I add a tighter and tighter mesh, the stress will continue to increase. This is why FEA isn’t a good tool for evaluating stresses in some cases.
When adding radii, I recommend a radius of no less than 1/8 of the slot width. To ensure that the tab will not interfere with the radii, add twice the radius to the slot length. This will have a looser fit, but give more strength.
Full Radius Slots
My “go to” for slot design is the full radius slot. By increasing the diameter to half of the slot width, I can minimize the stress concentration as shown below. The other benefit is that I can accurately calculate the stress concentration because it is in most tables.
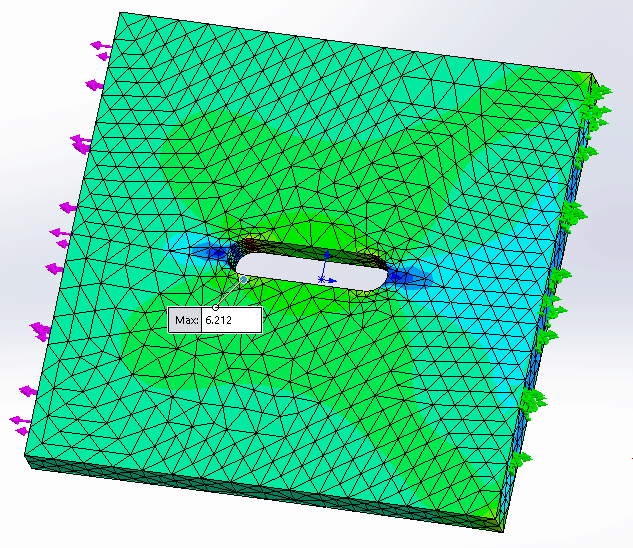
The major downside to this is that I lose even more lateral positioning accuracy. However, I have found in practice, that there are usually other parts that almost always add this accuracy back in.
The Dogbone
The Dogbone is a slot design that is used when highly accurate positioning is required. You will see this a lot in fixtures. This is usually used with a laser cutter because the tolerances are quite tight. A laser cutter will cut a very straight line, but as soon as it changes direction, you have imperfect corners. This is a problem in the corners of our slot.
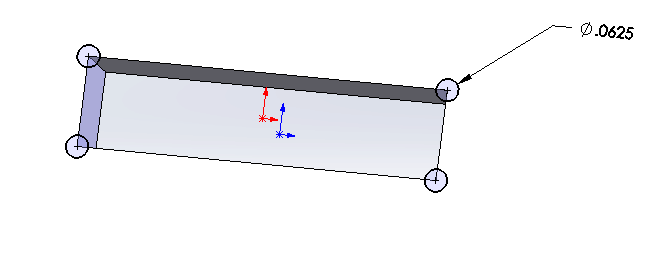
The solution is to add a circle at each corner and then blend in with a radius. The radius will usually be equal to the corner radius.
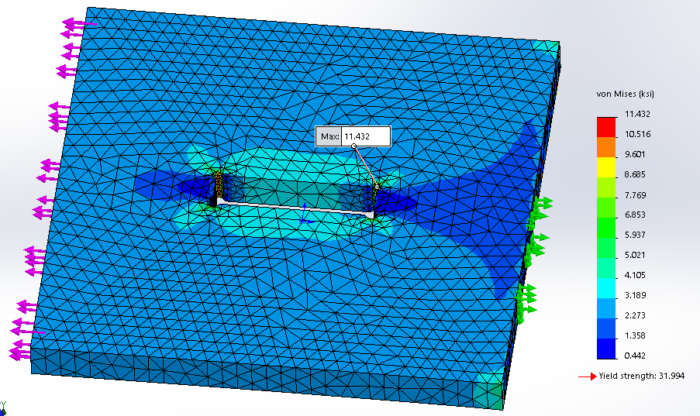
As mentioned before, there is a battle between accuracy and strength. This slot profile is very accurate, but creates the largest stress concentration.
The dogbone slot finds its best use in the design of fixtures, but can also be used in low stress applications where high precision is needed.
Tabs Aren’t Created Equal Either
Tabs are often overlooked for stress concentrations. In weldments where both sides of the plate are available for welding, it may not be an issue. However, in the case where only the tab is available for welding, there usually are very high stress concentrations.
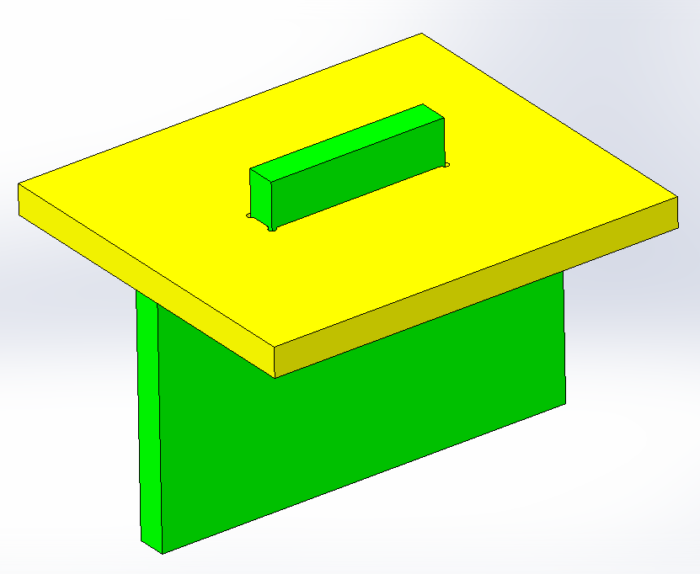
In fact, I don’t like to have tabs that stick all the way through the slot. Let me explain.
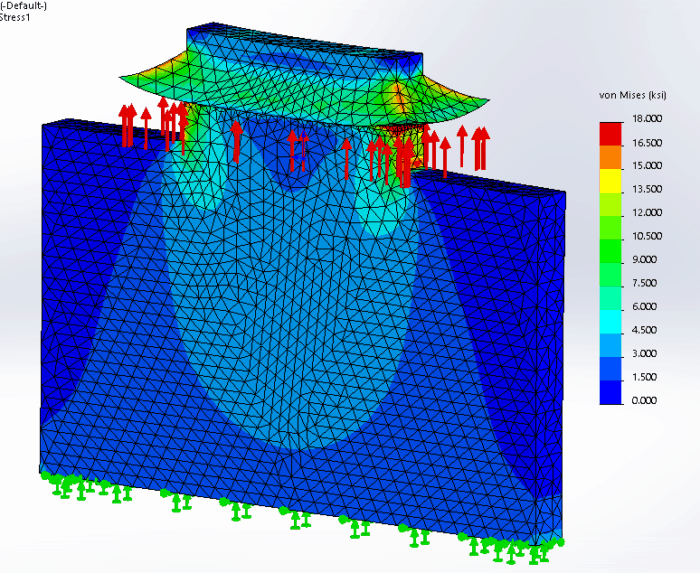
From the FEA plots above and below, you can see that there is an incredible stress concentration at the root of the fillet weld. This area is in tension and cannot be inspected. These are usually areas where fatigue cracks start.

Many people like having this design because even if the weld does crack, it will leave enough welded material so that it cannot pull through the slot. This is foolish for two reasons. One, the wedging action will induce major stresses on the slot that could cause the slot to tear. Two, good engineers don’t design things that fail.
Here are two options that will make tab design much better.
Modified Tab
By modifying the tab to be larger at the base and smaller at the top allows for much better stress flow. As you can see from the design below, the base is 1.50 in wide. Over the thickness of the slotted plate material, it tapers at 45° to a tab width of 1″. In this case, the plate thickness is 1/4″. I like using 45° because it allows the top of the tab to narrow by twice the plate thickness.
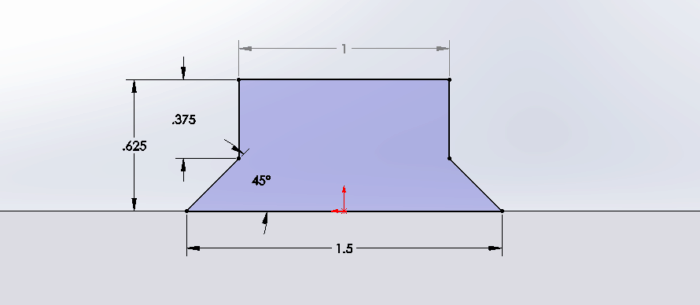
When we look at the FEA for a plate with only the fillet weld, we can see that the stress concentration is still under the fillet, but the stress flow into the tab is much more consistent. This is a win because we are now directing the stress flow the way we want to.
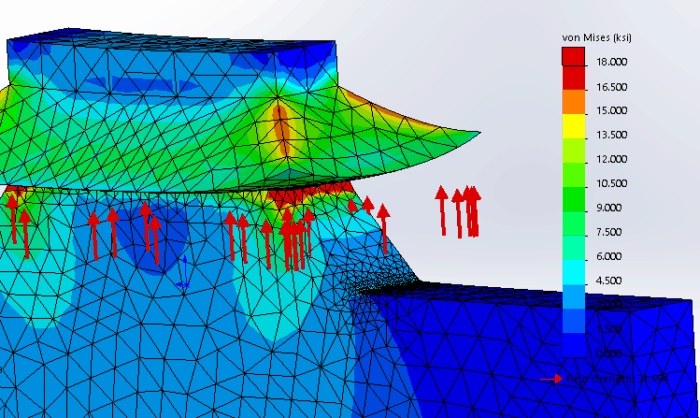
Now let’s take advantage of the cavity we just created by filling in the 45° taper with weld. That plug weld will give us a plenty of extra bonding between the plate and the slot and eliminates the stress concentration.

Minimal Tab
Even with the modified tab above, I have concerns about getting penetration deep into the bottom corners of the taper. My go to for a tab design is what I call the minimal tab. It offers the best joint for both the tab and slot.
As you can see below, the tab is very short in height and length. Usually it is less than 1″ long and 1/16″ high. It may need to be longer if the slot plate material is thicker than 1/4″ material.
By adding a plug weld in the entire slot, we ensure maximum penetration between the tab and slot. This fills in most of the slot with weld and removes most stress concentrations.
General guidelines for a plug weld is for the width to depth ratio to be greater than 1.5″. For example, a 1/4″ wide slot should have a maximum depth of 0.166″
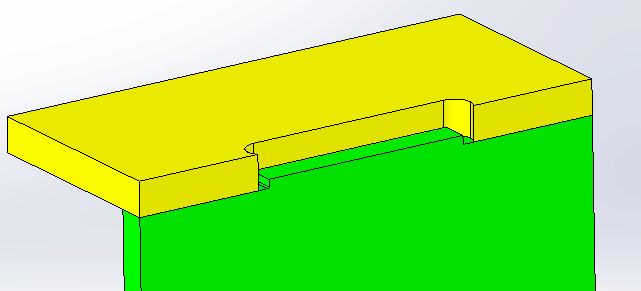
Don’t Believe That Filling in Gaps with Weld is the Solution
So a common misconception is that filling in the slot will regain the full strength of the parent material. Not True! While is may be true in a few situations, an engineer should never rely on 100% penetration of a weld. Instead, you should assume that there is no penetration on fillet welds and as little as 70% on bevel or plug welds.
There are many factors that go into this. The laser cut can leave debris, contamination or hard spots on surface making a poor bond with the weld. The welder can be having an off day and not position the nozzle correctly or not have the part “in position”. Using the wrong wire material, having the weld gas off or incorrect settings can lead to a poor weld.
Of course, you can grind out or plasma cut a fillet weld, but it is very difficult to clean out the inside surfaces of a slot or a bevel. For these reasons, we should never assume that our welds will fill in all the empty space of a slot.
Watch for Interferences
As a final warning on your tab and slot designs, you need to watch for interferences. Most of these interferences happen because the radius is ignored on both the tab and the slot. If the radii contact each other, the parts won’t sit properly. The general habit of a fabricator (including myself) is to hit that thing with a BFH (Big [um] Freaking Hammer) until it fits.
Since the interference is most likely caused by radii in contact with each other, you have probably mashed the nice smooth radius into a jagged surface. You just created a much larger stress concentration than the one you were trying to solve.
Make sure that there are no interferences on the tab and slots. Most 3D CAD packages have an interference detection module that points these out quickly.
Further Study:
How to Properly Design Weldments
Why Fatigue Cracks Start at a Weld and How to Diagnose the Cause
In Summary
All tab and slot designs are large stress concentrations. Follow the following guidelines and you can expect much better results.
- Determine the prevalent stress flow on your slots, run your tabs longitudinal to that.
- If your stress flows transverse to the needed slot direction, minimize the length of the slot.
- Be aware of the battle between tightness of joint and stress concentration factor. One must be sacrificed for the other.
- FEA doesn’t give you the best results because it assumes 100% penetration welds and singularity is almost always an issue.
- In highly stressed areas, use a fully radiused slot and a tab with minimal heigh
- Add radii to all corners and watch the interferences.
The Internet of Things Explained with Sealevel Systems
Why Calculus is Important for an Engineer
Many engineers see calculus as just a gateway to getting an engineering degree but it is so much more. Calculus is the math of the universe, explaining how all things interface together. Calculus is the foundation to even begin to understand physics, thermodynamics, materials, fluid mechanics, electronics and statistics. Without calculus, mechanical engineering wouldn’t exist!
At this point, everyone rolls their eyes at me.
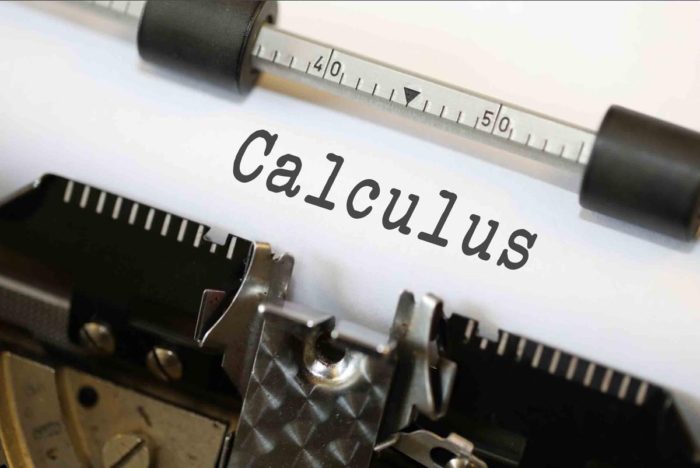
For me, I have designed nearly 100 different machines or machine subsystems. I can honestly say that I have performed calculus only 6 times on the job. Five of the six had to do with beam deflection and a seventh was used to determine if my water heater capacity was enough. (I know, I’m a nerd.) However, I have used the premises of calculus hundreds of times in design. Often times, the work of calculus has already been defined in tables. Whoo hoo!
History of Calculus
Calculus has it’s reaches back to ancient days as far back as the fifth century BC when mathematicians like Eudoxus tried to estimate the volume of shapes by dividing them into smaller and smaller shapes. The reason for small shapes is they are easier to calculate. He called this the ‘method of exhaustion’. We call this the ‘limit’ in modern calculus.
Archimedes was the first to pioneer integral calculus which he called ‘heuristics’ and use that to find the area of the circle by inscribing a many sided polygon. He found that as the number of sides increased it more and more approximated the area of the circle.
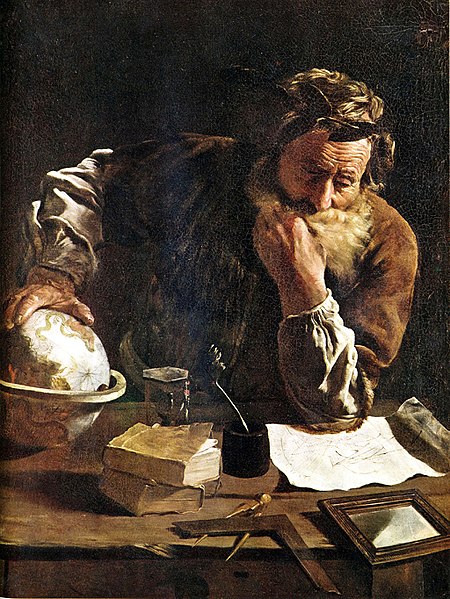
Modern Calculus
After these ancient discoverers passed on, calculus, sat dormant until the 17th century. At this point, Sir Isaac Newton and Gottfried Wilhem von Leibniz went on to formalize derivative calculus as we know it now. Surprisingly they worked on this separately each without knowledge of the other.
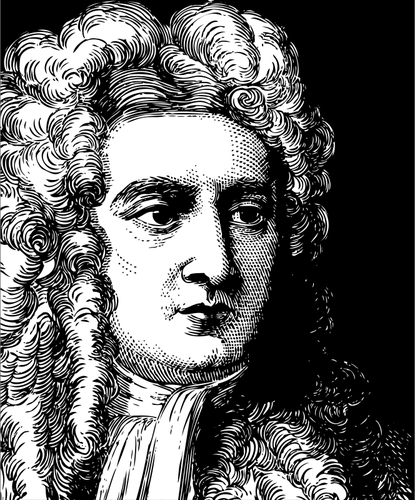
Isaac Newton studied why objects fall at an increasing rate of speed every second and why the celestial bodies will always orbit in an elliptical shape. He knew there was something behind these and needed a mathematical way of explaining it.
After mapping how an object falls over time he noticed that the curve was not linear and it kept increasing. He needed a way to find out what the velocity was at any given time.
Looking a distance vs time chart, he knew that if you drew a secant line near the point of interest, he could get a close approximation of the velocity. As the secant became smaller and smaller in length, will he get closer and closer to the tangent. The slope of the tangent line is the velocity.
This process above is known as derivative calculus. This is where we can find the slope at any point of any curve. In his research Newton found that the opposite of the derivative is the integral and that all of the information needed in a definite derivative could be switched back to an integral. This is also true and reverse.
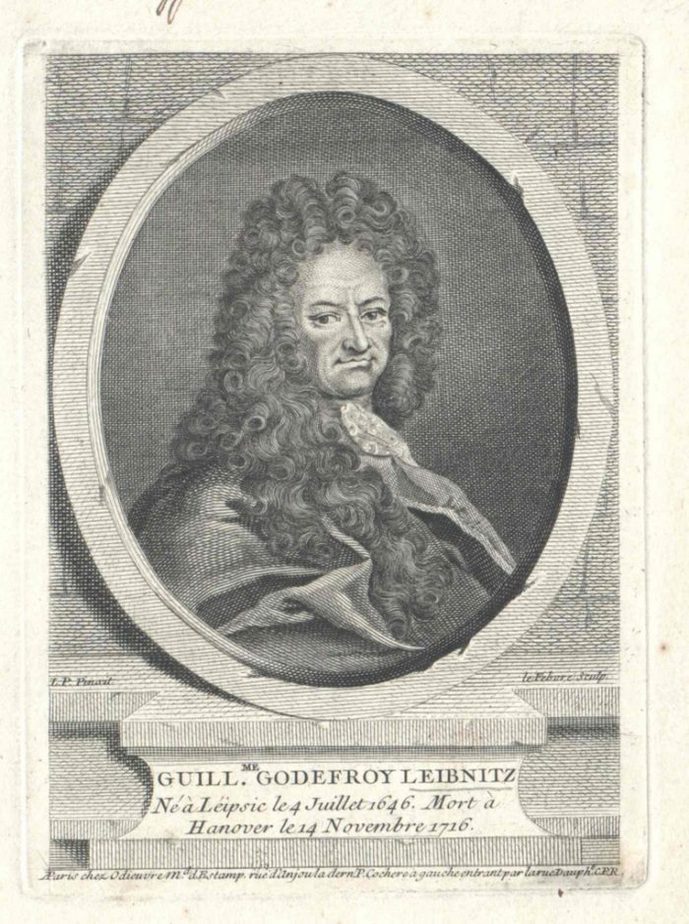
Leibniz and Newton’s developed and published their works separately and both had come up with integral and differential calculus at different times. In their publications, both of the mathematicians use different terminology but came up with the same fundamentals.
Two this day both terminologies of calculus are still used. Newton would puts a dot over the variable when a derivative was taken. For every derivative there were be another dot placed. Another alternative to the dot is to put an apostrophe afterward for each derivative. Leibniz uses the more traditional notation with the integral sign and the dx (or whatever the dependent variable is) after the integral.
What is Calculus?
Calculus can be divided into two parts: the derivative and the integral. The derivative is the slope of a curve at any one point. The integral is the area under the curve over a given range.
Before we can dive into those topics, we need to discuss the limit first.
The Limit
The limit is the process of dividing a function or equation into chunks. The smaller the chunks are, the better accuracy. For example, if we want to estimate the area of a circle by inscribing an equilateral triangle in it, you will have a very bad approximation of the area. As you increase the sides to 6 (a hexagon), your approximation gets better. If you go to a million sided polygon, your approximation is very good.
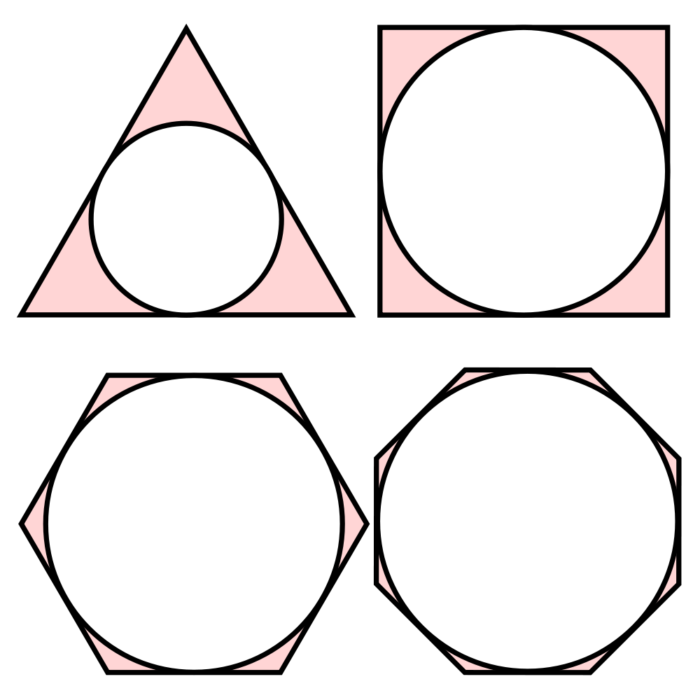
Image Courtesy of Braindrain0000
Another example of a limit is in (American) Football. If the offense is on the 25 yard line and the defense is penalized for ‘unsportsmanlike’ conduct (normally a 15 yd penalty), the ball will be placed half the distance to the goal on the 12.5 yard line and not the 10 yard line. If the defense keeps getting penalized every play, the ball will move closer to the goal line by half each time; 6.3, 3.3, 1.6, 0.8, 0.4, 0.2 etc.
The main thing to keep in mind here is no matter how many times the defense is penalized, the offense will never score. However, as the defense does get penalized, the offense gets a little closer to the intended “limit.”
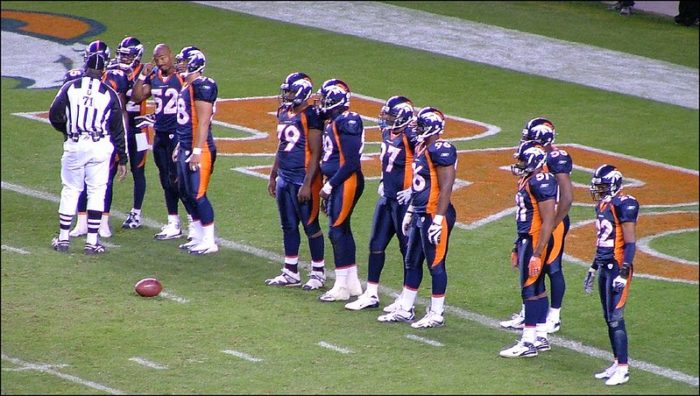
If we look at the equation below, we can see that the value of y when x = 0 is 0/0 or undefined. However, if we move just slightly to the right (or left) we see that the value of y is just less than 1.
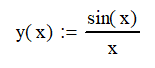
This is where the limit concept shines, we can find out values of functions at points that don’t really exist. The graph below shows the function from x = 0 to 10. You can see that as x approaches 0 from the right, the value of y is 1.
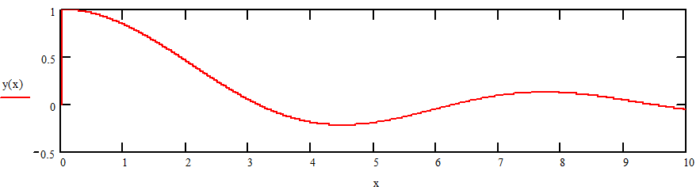
In calculus terms, we would express this as, “What is the limit of y, as x approaches 0.” If it is a discrete equation, you may need to evaluate the function “from the left” (meaning x values increasing) and / or “from the right” ( x values decreasing) to get the right answer.
Limits allow us to divide the function into smaller and smaller chunks of the function to evaluate things like slope and area.
Now let’s get on with the two parts of calculus!
The Derivative
The derivative where one can find the instantaneous slope or tangent of any mathematical function. This is great if we have a position vs. time chart and want to find the velocity (tangent) at any point. We can take multiple derivatives and find the acceleration (2nd derivative) and jerk (3rd derivative, yup its a real thing) of a function as well.
In any mathematical function, the derivative is found by taking a secant on the curve near the point in question. A secant is a line made through two points on a curve. Our interest in the secant is simple; it is very easy to find the slope of a line (rise / run). The points selected can be anywhere over the graph.
If we had a graph of the Dow Jones Industrial Average over the last 20 years, we might pick the points of today and 20 years ago and draw our line. We will probably find that the line slopes up.
If we are a stock analyst, this just won’t cut it because it is to general of an estimation. We probably want to look at the trend of the market between right now, and 5 yr, 1 yr, 1 mo, 1 wk, 1 day, 1, hr and 5 min. This will give us an good approximation of what the market is about to do.
We can then calculate the slope of the line for each secant and determine if the market is going up down or sideways.
Hopefully you noticed that our secant line got smaller and smaller in each step as we approach an infinitesimally small length of the secant line. As the length of the line approaches zero, the line will more and more represent a tangent line. This is what the derivative is.
There are many tables that have the derivative function for many common equation forms. These will have generic constants so that they able to be used in a wide variety of applications
The Integral
The other part of calculus is integration; this is where we can find the area under any curve. This is used if we had a plot of acceleration over time we could integrate to find the unit the velocity and then integrate again to find distance.
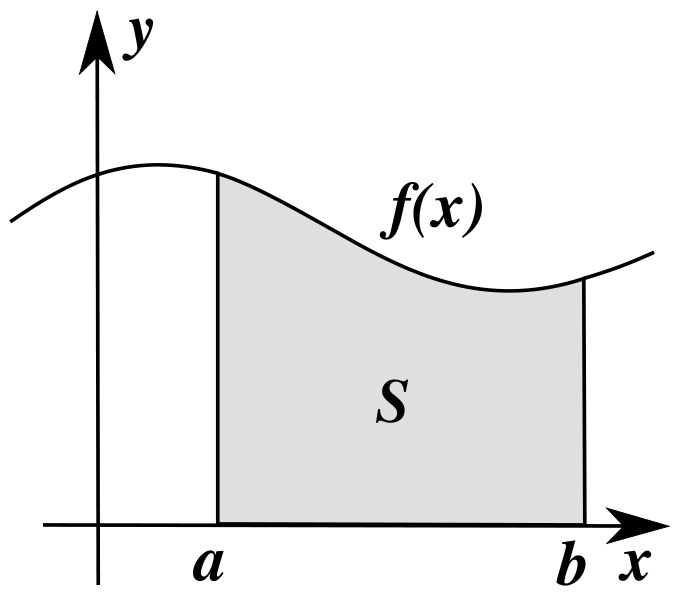
By dividing the area under the curve into smaller rectangular approximations, we can approximate the total area. As the number of rectangles increases, the accuracy of the result increases.
Quick shortcut: if you need to find the integral of a very difficult function, plot it out on paper. Then cut out the shape and weigh it. Compare this weight with a full sheet of paper. If you don’t have a scale that can read that small of a mass, you could also cut it on a laser metal cutter or print it in 3D.
Definite vs Indefinite Integrals
Not all integrals are created equal, there are two types; definite and indefinite. A definite integral has two points, 1 and 4 in the case below case, to evaluate after the integration is complete. The definite integral will always give a specific value as a result.

The indefinite integral is a little more fun. It doesn’t have a specific set of bounds so it gives a function (see right) instead of a specific value. With an indefinite integral, you will also have a constant, usually C, on the end of the integrated function. If there are multiple integrations done, the constants, C, would have subscripts (i.e. C1, C2 …Cn).
Once you get this far, we need to start applying boundary conditions to get the result we would like. In the equation above, we would only need 1 boundary condition.
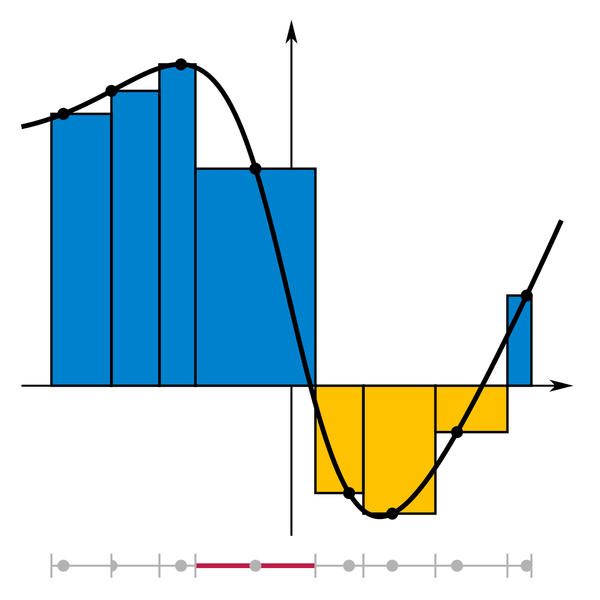
When dealing with beam deflection, you need to integrate twice so you would have two constants C1 and C2. As a result, you would need two boundary conditions per beam section. If this were a simply supported beam, we would say that the deflection at x=0 is 0 in and x=L is 0. These are our boundary conditions
Studies Past Calculus
Multidimensional or multivariable calculus is the next step, we may want to see how the function changes with respect to x, y, z, and time. Aeronautics is a great application of multivariable calculus as we need to know how fluid flows around an airplane wing.
Differential equations is also a must for the engineer. Differential equations are how we study radioactive decay, vibrations, electronics and how long you can shower before your water gets cold.
Differential equations is broken down into two sections, ordinary and partial. Ordinary Diff Eq, deals with only one dependent variable at a time while Partial Diff Eq deals with multiple variables. I did not enjoy this class at all.
Why Calculus is Important
Hopefully, it is plain to see that knowing the area under a curve for the slope and of a curve at any point is very important to an engineer. If you still don’t believe me here are some examples.
Meteorology -meteorologists use calculus to determine how wind will flow between a high and low pressure areas. As a high pressure area will force air to move to a low pressure area. We can determine the size and shape of these areas and determine how windy it will be.
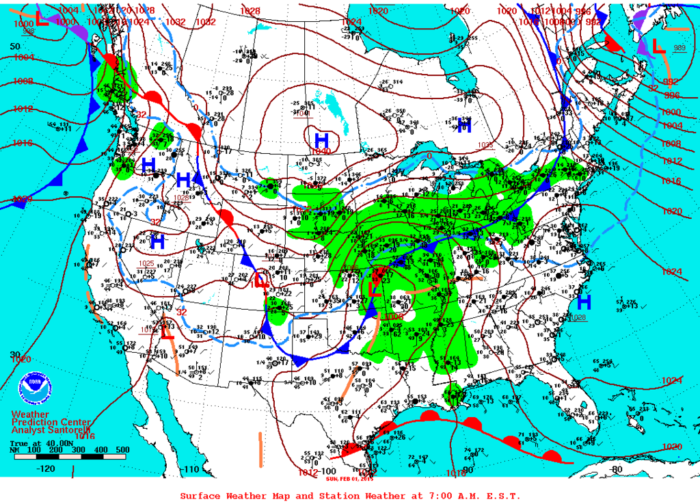
In physics, calculus explains how motion is controlled. We know that that the motion of a car can not instantaneously change position the velocity but motion speeds up and slows down gradually. Calculus is the tool that allows us to mathematically model motion.
Calculus is widely used in rocket propulsion. First at lift off, the rocket has a constantly changing weight because it keeps burning off fuel. Right at lift off, you need to burn more fuel than when you are near orbit. Calculus is also used to determine the gravity force as the rocket is further and further from earth. Finally, determining the speed and height from earth needed for an infinite orbit is found using, you guessed it, calculus.
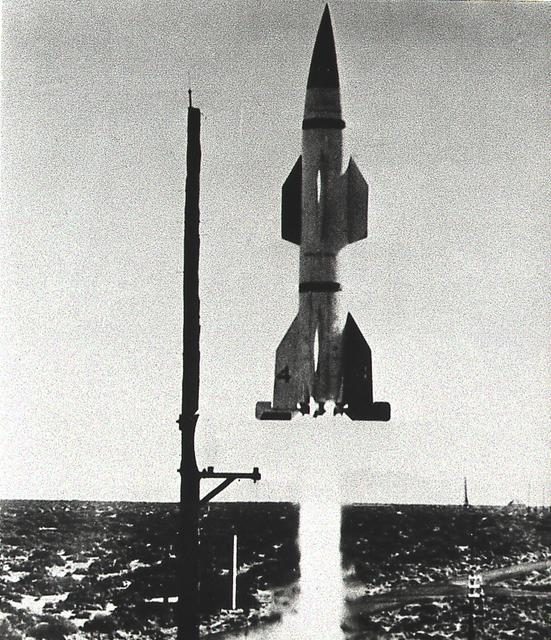
In structures we know that a suspension bridge is held up by cables that have a constantly changing slope. It is difficult without calculus to determine what the tension is on the cable at any point.
As mentioned, beam deflections are based off of the universal beam equation and requires a double integral for a solution.
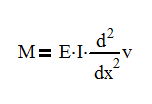
In electronics, we know that capacitors and inductors cannot charge or discharge instantaneous. Calculus is our bridge to understanding how fast a capacitor will charge. This is important to know because it affects switching speeds. If a capacitor takes 1s to go from 0V to 5V. We can only pass a 1 Hz signal through. If it takes, 1 ms, we can send a signal of 16 Hz.
Calculus also explains how heat will transfer through walls, fluids and in space. Coroners use the normal and actual temperature of a body as well as the ambient temperature to determine the time of death.
Fluid mechanics uses multivariable calculus and partial differential equations to govern all fluid motion using the Navier-Stokes equations. While these long and tedious equations can be approximated and simplified, all Computational Fluid Dynamics (CFD) is based off them and allows us to model fluid flow through many complex shapes like the inside of a hydraulic valve or airflow over an airplane wing.
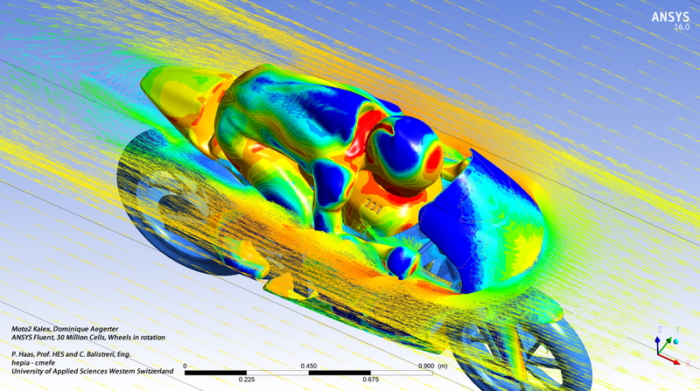
Other examples are in statistics where we can use normal distribution to gain confidence in how well our sample sizes represent reality. This is all calculus based. In economics, we use calculus to find optimum profitability in sales, supply and inventory.
In Summary
I have only scratched the surface on how calculus is used in real world everyday situations. Calculus is truly the natural language of the universe and understanding it will only lead to greater awe of this world we live in.