Check this Out
Hydraulic Symbols Template
Try the Ultimate Beam Calculator
Schedule Time with Corey
Recent Posts
Be a Better Engineer – Slow Down!
Office Chair Stability – Why Space is The Key
So why do tripods have 3 legs, kitchen chairs have four legs but all office chairs have 5 legs? The answer is simple, stability.
Office chairs have five wheel because it provides the most stability with the fewest wheels. Four or three wheeled chairs would need to have very long legs to have the equivalent stability. Chairs with more than five wheels have added cost with little extra benefit.
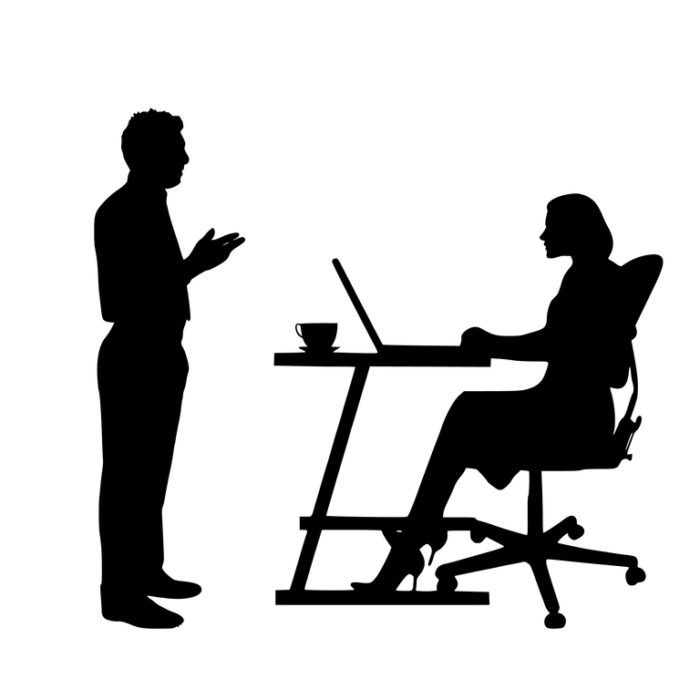
Defining the System
The first thing that we will need to do is define the system. We can say from experience, that no one has ever flipped over an office chair over the front, but almost always over the back and rarely over the side.
As a result, we will focus on stability over the rear of the chair. To determine stability, one thing we will need to know if where the center of gravity (CG) of the person is. The center of gravity of a person is around center of mass at the height of the ‘bee bo’, I mean navel.
In the image above, a woman is sitting in a standard office chair. The height is adjustable so there will be a range of heights used in our calculation. We will find that the height to the CG is around 30″ to 34″ (76.2 to 86.4 cm).
Office chairs are also designed so that the center post is in front of the CG by about 3″ to 4″ (7.6 to 10.2 cm). This is done for a few reasons. First, it prevents creaking and swaying in the joints. No one likes a creaking chair and if the load is offset, it will always be in contact and rarely go over center which is what causes the swaying sensation.
However, the chair is balanced side to side so that if you shift your weight, you will notice some play in the chair design. Chair manufacturers try to minimize this because there is no other solution. If you put the post to one side, the chair will not move as easily when pushed by foot.
The second reason is that the post is in front of the CG is it allows the rider to control the movement of the chair easier. This is because we want the weight of the operator will be leading the chair’s direction.
The CG can also be extended rearward when you lean back or push your legs down to rock back. We could make the assumption that the body’s CG will increase to around 8″ (20.3 cm).
We can then add dimensions to our picture so that we can start making our Free Body Diagram
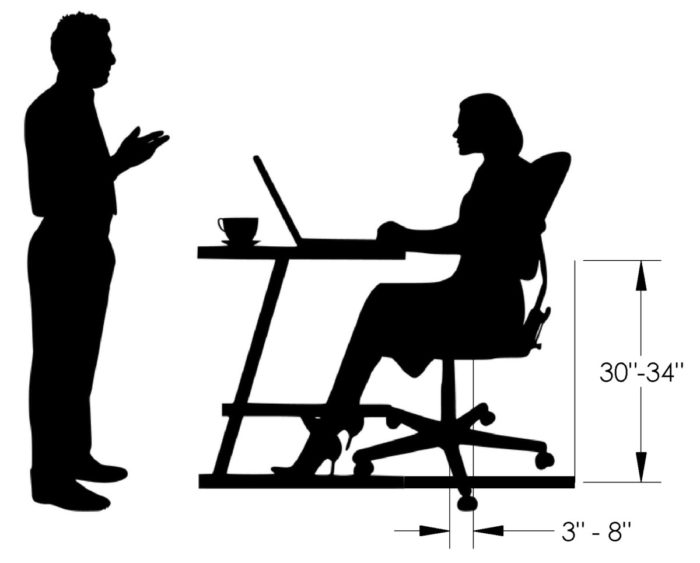
Dimensions added
Free Body Diagram
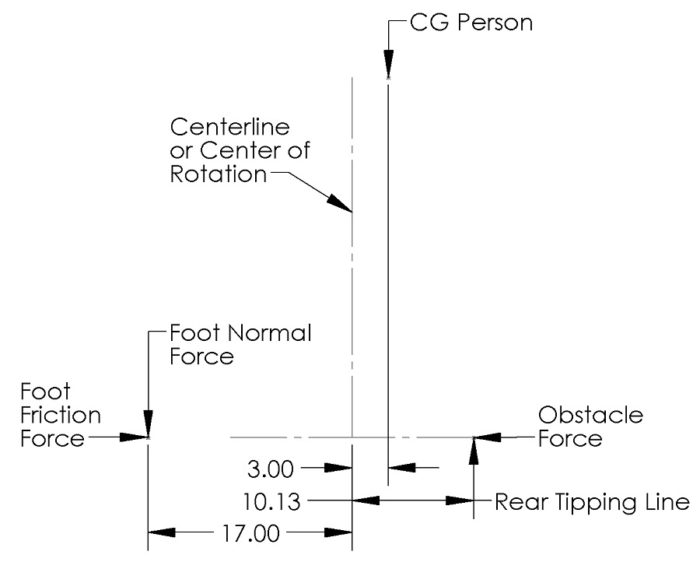
Case 1: Sitting in the chair
The diagram above shows the CG of the person and the rear tipping line. As you can see when we just have the weight of the user and no additional forces, the chair is very stable. The diagram above shows that the weight is clearly between the center post and the rear tipping line.
If you didn’t have confidence in the chair’s stability, we probably wouldn’t have sat down in it in the first place. No, the problem always happens when we start to move, shift weight and do other stupid things.
Case 2: Moving the Chair Backward into an Obstacle.
So this is the most likely way to make your chair tip over. So you are scooting your chair backward and you run into a jacket, purse, officemate’s foot or even the cheap plastic mat that your chair rolls on.
All of these items can make your chair less stable. Let’s put some numbers to an example. Let’s say that a 200 lb person encounters an object and 10 lbs of force will allow us to over come it.
The best way to approach this is to sum the moments at the rear tipping point and see if the moment is positive (meaning stable) or negative (meaning unstable). We will sum the moments with positive being a CCW moment.
The stability moment is the weight of the person from the tipping point. In this case it is: 200 lb x (10.13 in -3.00 in) or 1426 in-lb.
To find the Foot Normal Force we will need to make an assumption on the coefficient of friction between the rubber sole of your shoe and the floor. Depending on the type of shoe and floor material, I would guess that the coefficient could range from 0.2 to 0.7. Lower values will create larger normal forces, so we will use the 0.2 factor.
We can see that the Foot Friction Force needs to equal the Obstacle Force; 10 lb in this case. The Foot Normal Force can now be found by dividing the Friction Force by the coefficient of friction. The normal force will equal 10 lb / 0.2 or 50 lb.
We can calculate the moment that will cause instability by multiplying it by the distance to the tipping point. In this case, 17.00 in + 10.13 in. The moment is 1356 in-lb.
Is it Stable?
Well, we can subtract the stability moment from the instability moment. 1426 in-lb – 1356 in-lb = +70 in-lb. The chair is stable! You won’t fall over!
So Why Five Wheels?
Yes, back to the question at hand.
This question can be demonstrated far more easily with a diagram. The picture below shows the minimum tipping point of chairs with 3, 4, 5 and 6 wheels. You can see that as the number of wheels increases, the length of the leg decreases.

The reason we draw the line between the legs is when one leg comes in contact with an object, the chair will pivot (rotate) until there is a balance in force. This will be back to a static condition when a second wheel comes in contact with the object. At this point, the tipping line is the line between the two stuck wheels.
One other thing to note is that the wheels pivot on a location that isn’t at the center. This is so they are always lined up with the direction of travel. However, this off-center distance always works against us with regard to the tipping line. In the example above, I have already subtracted the off-center distance from the leg length.
Conclusions
We can see that having a three wheel chair is very impractical. We would need nearly double the leg length as a five wheel chair to have the same stability. This chair would be bumping into everything as we moved around and wouldn’t fit under most desks. Four wheels gets us close, but still it has long legs. On the contrary, going with a 6 wheeled chair only provides a slight leg length reduction, but would have a higher cost for the leg, wheel and center post design.
That is why office chairs have five wheels.
How to Design a Divot Free Roller System
How to Connect Multiple Valves Using Power Beyond Technology
Connecting multiple valves together is always a challenge. You want to have individual valve functionality, but not loose sight of the overall system characteristics.
Open center or through center valves need to be connected in series using power beyond porting. Power Beyond allows unused flow to power multiple valve sets downstream. Power beyond also allows the designer to choose which valve sections are more important than another.
In a hydraulic system, there can be multiple operator locations. For example an aerial lift device can have multiple control stations. Generally there is one in the platform and one at the base that controls the boom functions. There can also be multiple stations to deploy the outriggers to prevent the chances of bodily harm by having good line of sight.
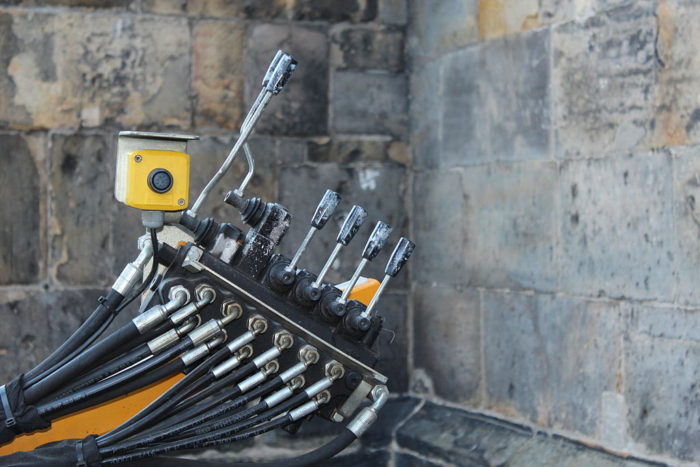
Mobile equipment like this is the primary use of a power beyond valve. It allows the operator to work at multiple locations while having the needed functionality.
Another benefit to power beyond systems is that you can change which functions are higher priority by choosing what order they are in the valve. In the aerial platform, we would want functions that move the boom lower priority than those that deploy the outrigger. (You want the outriggers deployed BEFORE you move the boom.)
When connecting multiple valves we need to address an array of topics to have good system design.
- Parallel vs Series Arrangement
- Open vs Closed Center
- Through Center vs Tandem Center
- Why not Tandem Center
- Priority Flow & Metering
Let’s get started
Open vs Closed Center
So the first thing to know is what is the difference is between open center and closed center hydraulic systems. This is identifiable in the hydraulic schematic.
The trick to this is to see if flow can return back to the reservoir when no functions are activated. If it can, the system is open center, and the system is sometimes called a full flow system. Beware, the path back to the reservoir might only be a pilot line and only uses about 1/4 gpm (0.95 lpm)
If the path to tank is clearly blocked, your system is closed centered. This system will either employ a pressure compensated pump or positive displacement pump with an unloader valve to prevent heat generation.
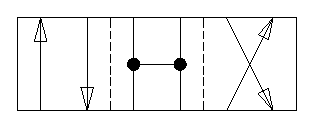
The top image here is a “open” center configuration where all of the ports are connected together. Other open versions of this would include the A and B ports blocked or a “motor” center where the flow is restricted from the work ports.
The image below is a closed center version of the image above. The only difference is the pressure (P) port is blocked so only flow from the work ports can flow to tank.
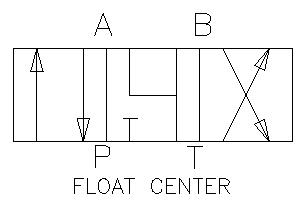
Open vs Through vs Tandem Center
An open (above) and tandem (below) center valve are pretty much the same thing. They allow the flow to move from pressure to tank. The main difference will be in how the work ports are connected.

A through center valve allows the flow to run right through the valve when it is in the center position. When the spool is shifted, the the through path will be blocked. Technically, this makes it a 3 position, 6 way valve, but I have never heard it referred to as anything but 3 position, 4 way.
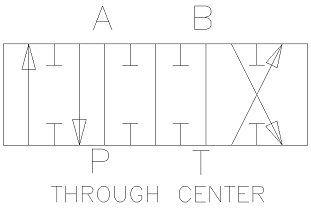
For a non-proportional valve, the flow will be blocked completely usually before pressure can flow to the work port. (it happens so quickly)
A proportional valve will meter the flow so that the opening size from P to the work port will match the opening of the through section. A lot of really smart engineers do CFD (computational fluid dynamics) to make sure that the openings in both cavities are matched for the desired outputs. Takeaway – don’t worry how it happens, just read the technical graphs they provide you.
Valve Cores
You may hear a salesman mention that the valve has a Y core or Z core through section. These are simply indications of how the flow goes around the spool when in the center position. Valve spools are round and have many notches and recesses in them. They also may have multiple tank port connections.
In a Z core configuration, the flow moves around the spool in a Z shape. This means that the pressure moving around the spool will push on only one side of the recesses causing the spool to shift one way due to pressure differential. To resist the spool from moving, heavier springs are used to keep the valve in the center position.
With the heavier springs, the operator may notice that the valve may shift easier one way. It may be a slight drawback.
A Y core configuration solves this problem by splitting the flow (in the shape of a “Y”, gasp) around the recess making the pressure differential to cancel out. This results in a balanced spool and the ability to use smaller centering springs.
Why We Don’t Use Tandem Centers
The problem with tandem center valves is that when multiple valve sections are used. I detailed this problem in another article, but I wanted to do a quick summary here as well.
Pressure Intensification
In the below configuration using tandem center valves, you can actually get higher pressures. This can cause damage to components to the structure or worse; bodily harm.
This can happen when the lower directional valve is moved so the P goes to B and A goes to T. Because of the cylinder ratio (bore side area / rod side area), let’s say it is 1.5:1 we can actually build up 1.5 times the system pressure on the A work port. This pressure then goes to the second (top) valve.
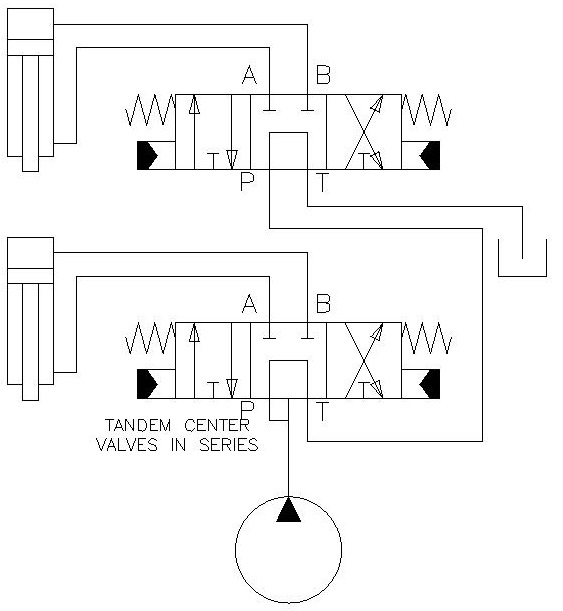
Most hydraulic systems don’t have relief valves between the sections so there is no protection on the system. Also, you can intensify the pressure the more sections are in your system.
Other issues are low pressure and a limited supply of oil. Low pressure can occur when the first section is shifted the other way connecting pressure to the A port. Here the cylinder ratio works against us.
Finally, the cylinders only have a limited supply of oil. Once the cylinder is out of stroke, there is no more oil for any of the downstream valves.
Tandem center valves are not the solution for using multiple valves on an open center hydraulic system.
For more information on tandem center valve, please read my article and watch this video.
Through Center Valves
As mentioned previously, adding a path through the center of the valve spool allows much better control off the downstream flow and pressure.
In the figure below, the as the first (bottom) valve is shifted, the flow is cutoff to the second valve. If it is non-proportional, there will be no flow to the next section. If it is proportional, the flow to the next section will be reduced by the amount the valve spool is shifted.
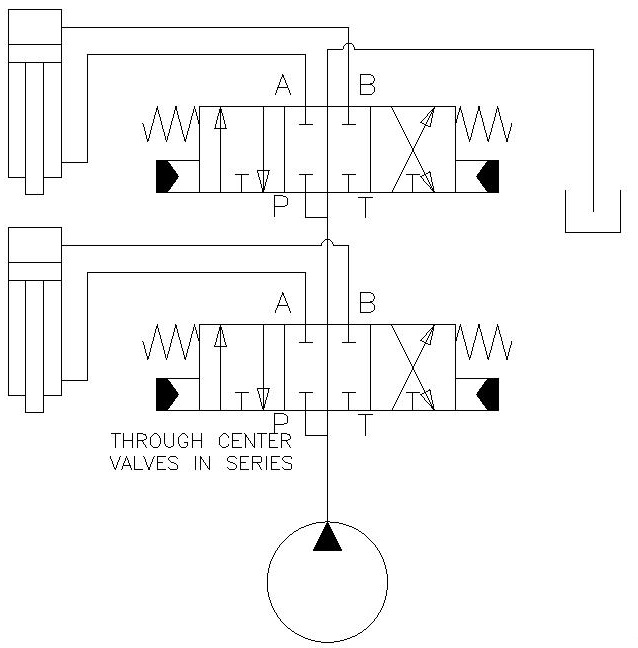
Parallel vs Series Arrangement
Parallel Arrangement
Now that we have defined, open and closed center systems as well as which center sections to use, we need to learn how to combine them.
Most of us have indoor plumbing and we can identify that it is a closed center system. This is because each faucet or appliance is at the end of a branch stopping flow when shutoff. If all of them are shut off, the pressure builds until maximum pressure is built.
Household plumbing is a closed center system and we need to attach all of the faucets in parallel or on their own branch for proper functionality.
Most industrial hydraulic applications work this way where many valves can be added in parallel to the pump pressure.
What Happens If We Add One Open Center Section?
If we were to add only one open center section to our system, none of the closed center valves would function as intended. The system is now an open center system and flow would pass through freely. This changes if the open center valve is blocked and allows pressure to increase.
Below is a good example of how to combine an open and closed valve system. The working valves are closed center, but there is an unloader valve (S7) that is energized only when one of the other valves is energized. This allows us to use an inexpensive gear pump but operate closed center valves.
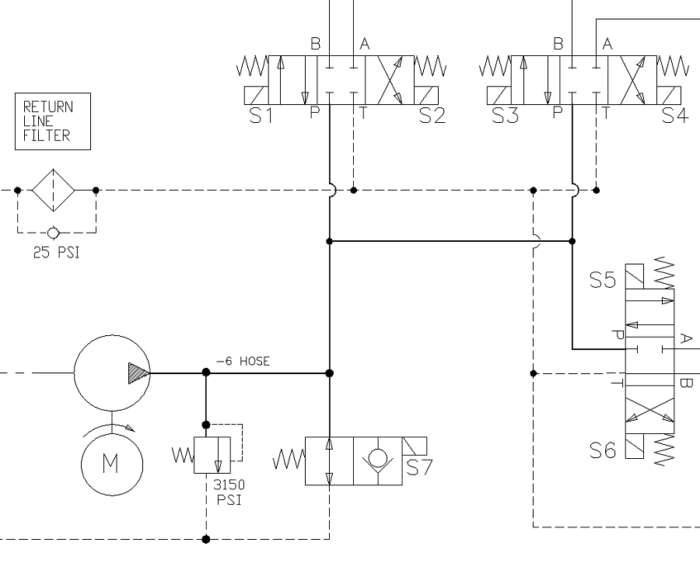
The schematic shows that all oil is blocked at the three directional control valves, but can flow freely to tank if S7 is not energized. Energizing any of the other valves (S1 – S6), will do nothing if S7 is not energized.
Series Arrangement
Looking at the above example, if we were to change all of the closed center directional control valves to open center, you will have multiple paths for the oil to flow. To make the machine do anything, you would need to energize multiple things to get any action.
Action = S7 and (S1 or S2) and (S3 or S4) and (S5 and S6)
This combination is probably not what your desired use of the hydraulic system. Rearranging the valves in series is your solution.
I Thought This Article was About Power Beyond?
It is and we have already introduced the concept with out mentioning it by name. Revisiting the through center schematic from before, the power beyond is the line that connects the two directional control valve.
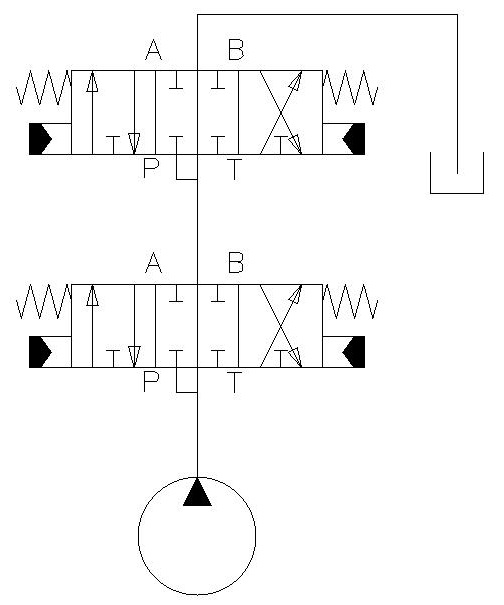
In a tandem valve center, there are only four ports on the valve; pressure, tank, A and B. The through center adds a fifth port; power beyond.
If this was a sectional valve or monoblock valve, the power beyond is handled internally and there is no need for additional porting. However, if you have multiple valves at multiple locations the power beyond requires an additional port.
Every open center valve is made with several, minimum 2 and usually 3 tank ports all sharing the same cavity. Part of the reason is for convenience, but one of these can be used to insert a Power Beyond plug.
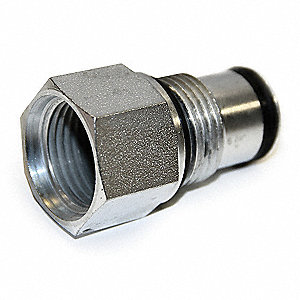
The valve and spools are designed to have the power beyond flow and the tank flow separate and then combine in the tank cavity. The image shows an o-ring the far right side. When screwed into the correct port on the valve, it will divert the power beyond fluid to this port and not to the tank cavity.
This plug gives us high pressure fluid that can power additional downstream valves.
Side note: It is important to not block this port during normal use. It is difficult to relieve the pressure from it.
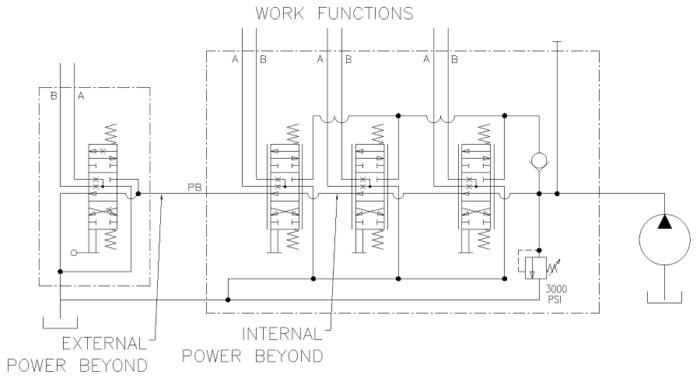
This schematic shows the use of power beyond in between sections and between multiple valves.
Priority Flow
In the schematic above, you can see that the first valve will get all the flow. The remaining valves will only get the remaining flow. If there are many valves, this can lead to unpredictable or no flow for the last valve(s).
This can be both good and bad. It is bad in the way that the flow is unpredictable. It is good in the sense that we can control processes and set priorities in the system.
In the case where there are multiple control stations, we can set the importance of each one. With the aerial lift we could set the priority to be outrigger station(s), lower controls, upper controls. Each one has the ability to override the downstream controls.
A machine with multiple e-stops could also benefit from power beyond. Each emergency stop could divert flow to tank preventing the operator from getting hydraulic pressure and flow necessary to perform work.
Finally, there may be functions that you just don’t want operational while other functions are active. When moving an aerial lift, you may not want the platform to adjust the tilt. The use of power beyond can minimize or eliminate this hazard.
In Summary
The use of power beyond is a wonderful tool to have in your hydraulic belt. It allows the use of multiple valve sections or blocks without the disadvantages of using tandem center valves that plumb the Tank port of one valve to the Pressure port of another.
We also have the advantages of setting priorities in the use of hydraulics for an open center system which allows us to control what functions are available in certain configurations.
Best Reference for the Mechanical Engineering P.E. Exam Review
How to Determine a Cylinder Bore Diameter Without Disassembly
Many times in my career, I have found the need to determine a cylinder’s characteristics from an assembled machine. This is often the case when scoping out the competition. Most critical dimensions can be found with a tape measure in a matter of minutes. The cylinder bore cannot.
Determining the bore or inside diameter of a hydraulic cylinder without disassembly is possible by measuring the barrel outside diameter. The wall thickness can be estimated using Barlow’s formula Finally, the bore can be calculated and then compared to common cylinder bore sizes.
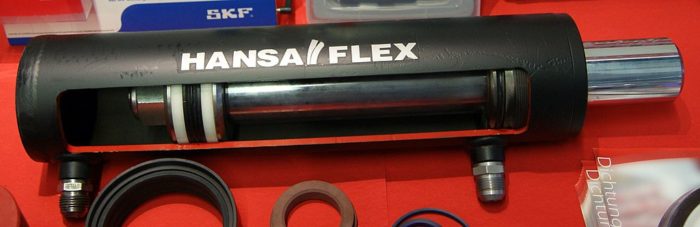
So measuring the rod diameter, retracted and extended length of a cylinder is easy. It is far harder to take the cylinder apart and measure the ID. (It is by far very messy as well and you could damage the cylinder). Even with the giant cutout in this cylinder, getting an accurate measurement is tough.
Furthermore, it is quite unnecessary as well. Keep you hands clean and simply measure the barrel outside diameter.
Determining System Pressure
Knowing the system pressure is a critical first step to determining the bore ID. Most hydraulic systems operate in the 2400 psi to 3000 psi (165 to 207 bar) range.
We can look at the hydraulic hoses for pressure ratings on the inlay, but that can be misleading. A hose that is rated for 4500 psi (310 bar) can be used on a 2400 psi system with no issues. You may have better luck with this method if your cylinder uses thermoplastic hoses.
If the machine doesn’t have a pressure gauge already mounted on it, get one and install it. Often there is a location where a quick connect fitting is ready for a gauge. I recommend using one that goes to 5000 psi in case the pressure is higher than the expected location.
Once the gauge is installed, power one function so that a cylinder is either fully extended or fully retracted. This will cause pressure to go over relief and our gauge will indicate the maximum system pressure. Make sure that the function selected won’t damage the machine and it doesn’t have any pressure reducing or limiting valves on it.
Measuring the Barrel
Accurately measuring the barrel can actually be a little challenging. On an assembled machine, there my not be adequate access to the cylinder where the aren’t ports, feeder tubes, or welds. Perspective also makes it difficult to get an accurate reading of the barrel diameter. With these two issues, using a tape measure to determine the barrel size may be out of the question.
Measure the Circumference Instead
Measuring the circumference is often a better way to measure the barrel diameter. You only need limited access and you can line up the numbers easier. If you have a ‘pi’ tape measure (reads diameters when wrapped around circumference), use it. Otherwise use a standard tape measure.
I recommend using a 1/2″ (13mm) wide or less tape measure so that the arc across the tape measure lays flat and doesn’t interfere much with the measurement.
If you only have a 1″ (25 mm) wide tape measure, I would suggest turning the tape measure over so that the numbers are on the inside. This way the tape measure lays flat against the barrel much better.
For either type of tape measure, I also burn the first 10 inches of the tape. By not using the first 10″ of the tape, you prevent the end clasp from interfering with the measurement. You could use as little as 1″, but I often forget to subtract that from my measurement afterward. Ten inches is a little more obvious that something is wrong.
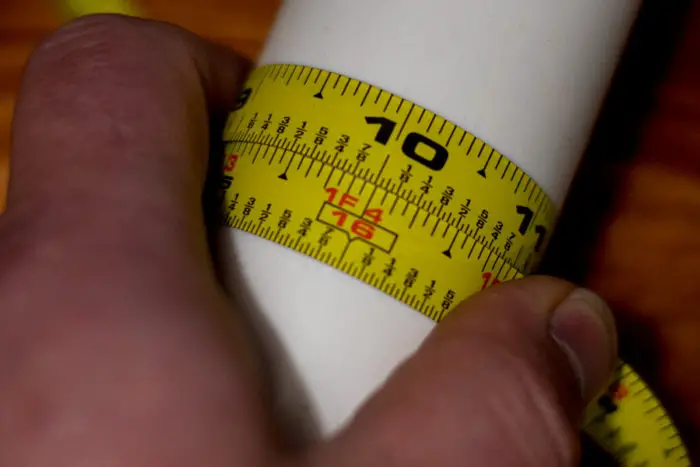
When measuring, line up the tape measure as shown and read the value where it lines up with 10″. Then subtract 10″ and divide by Pi to get the circumference.
Determining Wall Thickness
A key element of determining the wall thickness is determining the tube’s material strength. Most tubing used in cylinder manufacturing is high strength tubing that has a tensile strength of 101.5 ksi (700 MPa).
Yes, some manufacturers use even higher grade steels, but this is rarer than we think. When considering cost and strength, it is a good assumption to use this material.
Design Factor
Since cylinders are often used in overhead lifting or lifting of human life, they are designed to a 3:1 design factor at minimum on burst strength.
Some design standards require a 4:1 design factor on burst pressure. There are many reasons for this high design factor:
- Loss of life if failure
- Temperature increases (makes oil less dense and increases pressure)
- Cylinder may be loaded to higher pressure than system pressure
- Induced loads
- Shock loads
- Axial loadings
Ultimately we don’t want the cylinder to fail if the pressure increases by a significant amount. So we use a 4:1 design factor.

Barlow’s Formula
Barlow’s equation is a simple formula that measures the circumferential or “hoop” stress of a pressure vessel. This equation accounts for the pressure, average diameter and wall thickness.

There are differing opinions on whether the OD, ID or midplane of the tube should be used for this equation. Most use the mid-plane diameter so we will use that here. It is shown as (OD – t) in the middle equation.
The second equation (right) is the same only rearranged to give us the thickness, t, without using an equation solver.
Once we have the thickness, we can find the bore by the following equation.
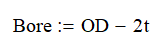
Pulling It All Together
Now once we have the bore diameter, we have to make some judgement calls. This calculation is theoretical and you will come up with a very specific answer. It won’t be the actual diameter of the bore, but it will be close.
Minimum Thickness
Cylinder manufacturers will generally limit the minimum thickness to around 3/16″ or 5 mm. This prevents dents and dings on the surface from causing issues with the seals. It also limits thermal issues, addresses axial and buckling loads. It is also easier to handle and store.
Common Bore Sizes
Cylinder bores come in standard sizes which mean that they are somewhat predictable. They are 1.5, 2.00, 2.50, 3.00, 3.50, 4.00, 5.00, 6.00, 7.00, and 8.00. Greater than 8″ cylinders usually step up in 2″ increments.
These are not the only cylinders bore sizes available. I have seen and used a 4.25″ and 4.50″ cylinder.
Two Quick Examples
If I measure a cylinder that is 4.50″ and another that is 2.94″, what are the bore diameters? Both cylinders see system pressure of 3000 psi.
Let’s start with the 4.50″ cylinder.
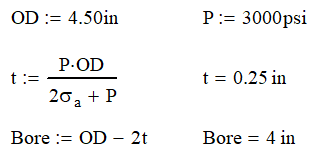
You can see here, that the bore calculated is exactly 4.00 in, that rarely happens. We can conclude that the bore is 4.00 in. If the diameter was a little larger or smaller, we could make the same assumption.
Now, the 2.94″ cylinder.
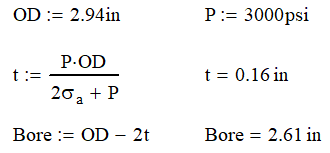
Our bore is calculated to be 2.61 in. We can see that the thickness is 0.16 inches which is smaller than the minimum thickness. When we increase the tube wall thickness, we get very close to a 2.50 inch bore diameter. We will use that.
Conculsion
With a simple measurement and few quick calculations, we can determine the bore diameter of a cylinder without ever looking inside. Knowing the tensile strength and the system pressure can get us close enough to accurately determine how powerful a system we have without disassembling the cylinder.