To quote my mentor, C. Marvin Franklin, “Bolts are Magic.” This is true! In the world of engineering, bolts simply are magic. They allow us to complete many projects and serve us in a variety of ways, which are vital in everyday applications.
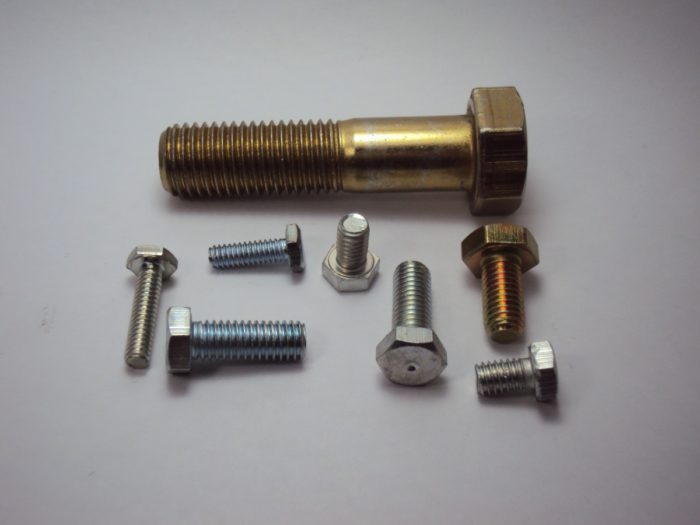
For the most part, structural bolts are made of steel and steel corrodes. Depending on the environment, other materials like brass and stainless steel corrode to.
Steel is the material of choice and if we want it to last, it needs some protection. This protection comes in the form of platings and coatings. The most common are zinc, galvanized and black phosphate.
Characteristics of a Good Plating
A bolt’s number one enemy is rust, since the overwhelming majority are made of steel. Most steel fasteners have some sort of coating on it which will turn white or gray, but the type of corrosion that we are concerned with is called ‘red rust.’ This is when the steel starts to corrode.
The method for evaluating the time to red rust is by using a salt spray chamber. In this chamber, a fine mist of salt is sprayed on parts continuously. Once red rust appears, the test is complete and the hours are logged.
Generally, exposure to chemicals or other substances that cause rust within 50 hours is not a good coating for general outdoor applications. Once you are able to get around 100 hours without rust occurring, then you are getting some good use out of that bolt.
In the salt spray test, the white or gray is a lesser type of corrosion that doesn’t directly lead to failure. It is simply materials other than steel corroding first. This corrosion order is based on the galvanic chart.
And there are a lot of choices out there. Doing a search on McMaster Carr, there are 36 different platings for fasteners available. So, there is a lot to choose from.
Some of these platings are simply non-starters because they cost too much. Gold and silver platings fit here, but they are also undesirable for corrosive environments because they are too noble. Let me explain.
Galvanic Corrosion
Different metals are more noble or rust resistant than others. When dissimilar metals are mated together, they form a battery. As a result one will always corrode before the other.
We’ve all see a corroded battery terminal. This is caused by dissimilar metals. This is also how thermocouples function. The wires of dissimilar metals will create a current and we can measure that current and get a temperature

This is why underground propane tanks have a copper wire attached to a large chunk of zinc. The zinc will corrode before the steel in the tank will. Since our parent material is steel, to get the best rust prevention, we would want to use substances that don’t interact. If we went to a more noble material like gold, not only would the fastener cost a fortune, but it would essentially rust from the inside out. We definitely don’t want that to occur.
The game here is to have a coating on the fastener that will corrode before the steel parent material, but also give plenty of time for it to corrode. Oh, and we do not want to interfere with the thread fit or fastener friction and it must look pretty at the same time. You can see that this is not an easy task!
Plating Processes
Electroplating
Electroplating is a method of transmitting the plating to the parent material using electricity. This process takes place when a beaker is filled with water and a piece of zinc material with the bolt is placed into the water. Beside the beaker of water is a battery with the positive terminal attached to the zinc and the negative terminal attached to the bolt. Eventually, the surface material of the zinc is deposited onto the bolt. Depending on how long you continue this process and the rating of voltage used will determine the thickness of the plating the bolt. Obviously, if you are making these by the millions, you aren’t using a battery and a beaker, but you get the idea.
Electroplating isn’t without its issues. For high strength bolts, generally higher than grade 8, electroplating introduces the issues of hydrogen embrittlement and stress corrosion cracking. Read this article for more information on those.
The electronic process introduces hydrogen or other electrolytes into the fastener that severely weaken the fastener. This risk is mitigated by “baking” the fasteners after the plating process to remove the hydrogen.
Hydrogen Embrittlement was a major issue back in the 1980’s and led to the Fastener Quality Act of 1990. This act put requirements for manufacturer identification, accreditation and testing.
Mechanical Plating
Many manufactures avoid the use of electroplating altogether for high strength fasteners by mechanically plating them. This is a process where fasteners and the plating material (usually zinc) are tumbled in a drum until the zinc is embedded on the fastener. For a visual cue, imagine throwing zinc and some screws into a cement mixer.
Vapor or Vacuum Plating
Another way to avoid the use of electroplating is to vacuum plate them. In this process, parts are loaded into a chamber and the pressure is reduced far below atmospheric pressure. The metal to be deposited is vaporized using a filament. The material will then flow onto the base material. This process can be repeated several times with different materials such as cadmium with a top coat of hexavalent chrome.
Common Platings
I did a search on McMaster Carr for different platings for screws and found that there were 36 different available finishs for a screw. That’s a lot. Let’s focus on the widely used ones.
Trivalent Chrome Zinc Plating (White Zinc)
When we think of zinc plating, for the most part we are thinking of trivalent chrome zinc plating. This is also known as white zinc plating where it has a layer of zinc and then a top coat of trivalent chrome. It is the go-to finish, but it doesn’t offer a great resistance to corrosion. You will find this in your local hardware store.
In an outdoor application you may get 12 months use out of the fastener before you see red rust. (Ask my lawnmower deck.)
Hexavalent Chrome Zinc Plating (Yellow Zinc)
The next step up is hexavalent chrome to increase the salt spray life. The hexavalent chrome version, also known as “yellow zinc”, offers far better protection, but it has landed on the RoHS list. It is still readily available, but in the not too distant future, it will go the way of the Dodo. You may remember that the movie Erin Brockovich was about the use/misuse of hexavalent chrome (it’s a good movie, I recommend it)!
These fasteners are readily available from manufacturing suppliers like Fastenal, MSC and McMaster Carr. Buy from these vendors rather than going to the hardware store.
Hot Dipped Galvanizing
Another method of rust protection is called galvanizing. This is essentially putting larger amounts of zinc at high temperatures on the fastener. It can be expensive and hard to work with as you must use a different torque for it and it is a class 1 thread that requires class 1 nuts. Unless you are looking at severe exposure, it is preferable not to use this material.
Cadmium Plating
Cadmium plating is widely used in the military and aerospace industries. It is a great sacrificial coating for the steel, but it doesn’t have galvanic characteristics like zinc does. The combination of the two materials doesn’t form a battery that enhances corrosion.
Cadmium can also be used with chromate top coats (Trivalent or Hexavalent) and it can be applied through electroplating or vacuum plating.
The major downside to the use of Cadmium is it is a natural toxin like lead and mercury and is on the RoHS list. I do see that this plating will be around for a long time. The military and aerospace industries don’t like change and to mitigate risk, it will take a long time to implement. I can’t blame them; there are many lives at stake.
Black Oxide
Black oxide is probably one of the worst coatings out there. It corrodes very quickly outdoors. This is unfortunate because it actually give rise to one of the biggest issues of plaguing the fastener industry; the socket capscrew.
Socket head capscrews are all grade 9 (high strength) fasteners AND class 3A threads (tight tolerance) according to the governing standard. As a result, black oxide is the go-to plating because it is cheap and doesn’t add much thickness. As a result it doesn’t mess up the thread tolerance.
As more and more of these fasteners have moved from the inside industrial space to the outside world, better platings are needed. However, the thread class prevents using mechanical plating techniques and the high strength of the material prevents reliable electroplating due to hydrogen embrittlement.
Many suppliers will not warranty electroplated socket set screws. Some will not sell them and others demand a signed form releasing them from liability.
I have a feeling that by 2030, the governing standard will be relaxed to offer the fastener in a class 2A thread and / or a grade 8 strength as well as the current offering.
Where We are Going – Coatings
We also have coatings which are specifically designed to go on the bolt itself. These are made in the process called spin-dip which is similar to mechanical plating.
Since they are not electroplated, there is no risk of hydrogen embrittlement. You can get them in a variety of colors and there is opportunity to add lubricity to the threads. Coatings tend to have a very high salt spray life upwards of 1,000 hours. However, it is important to note that they are thicker and can disrupt your friction factor on the bolt.

Some of the major players in this market are Geomet and Magni.
These coatings are the growing trend in fastener technology and is the direction all major users of fasteners are headed. Unfortunately, if your quantity is not high, you probably won’t be using these anytime soon. Right now, these coatings are a premium and are used for critical applications where failure is not an option.
Conclusion
In this article, we have explored the main finishes for fasteners and discussed the pros and cons of each material and process.
In my design work, I avoid the use of fasteners higher than grade 8 and prefer the use of the yellow zinc plating. My second choice is hot dipped galvanized followed by cadmium.
While I welcome the coming movement of coatings, I still see it being at least 15-20 years before it reaches the general population.